TR2011-082
Finding a Needle in a Specular Haystack
-
- "Finding a Needle in a Specular Haystack", IEEE International Conference on Robotics and Automation (ICRA), DOI: 10.1109/ICRA.2011.5979857, May 2011, pp. 5963-5970.BibTeX TR2011-082 PDF
- @inproceedings{Shroff2011may,
- author = {Shroff, N. and Taguchi, Y. and Tuzel, O. and Veeraraghavan, A. and Ramalingam, S. and Okuda, H.},
- title = {{Finding a Needle in a Specular Haystack}},
- booktitle = {IEEE International Conference on Robotics and Automation (ICRA)},
- year = 2011,
- pages = {5963--5970},
- month = may,
- doi = {10.1109/ICRA.2011.5979857},
- url = {https://www.merl.com/publications/TR2011-082}
- }
,
- "Finding a Needle in a Specular Haystack", IEEE International Conference on Robotics and Automation (ICRA), DOI: 10.1109/ICRA.2011.5979857, May 2011, pp. 5963-5970.
-
Research Areas:
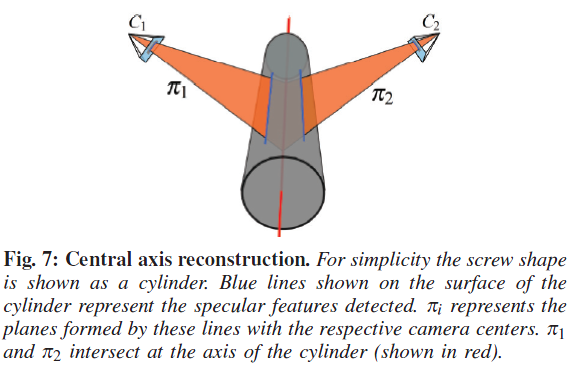
Abstract:
Progress in machine vision algorithms has led to widespread adoption of these techniques to automate several industrial assembly tasks. Nevertheless, shiny or specular objects which are common in industrial environments still present a great challenge for vision systems. In this paper, we take a step towards this problem under the context of vision-aided robotic assembly. We show that when the illumination source moves, the specular highlights remain in a region whose radius is inversely proportional to the surface curvature. This allows us to extract regions of the object that have high surface curvature. These points of high curvature can be used as features for specular objects. Further, an inexpensive multi-flash camera (MFC) design can be used to reliably extract these features. We show that one can use multiple views of the object using the MFC in order to triangulate and obtain the 3D location and pose of the shiny objects. Finally, we show a system consisting of a robot arm with an MFC that can perform automated detection and pose estimation of shiny screws within a cluttered bin, achieving position and orientation errors less than 0.5 mm and 0.8 respectively.
Related News & Events
-
NEWS MERL researcher, Oncel Tuzel, gives keynote talk at 2016 International Symposium on Visual Computing Date: December 14, 2015 - December 16, 2015
Where: Las Vegas, NV, USA
Research Area: Machine LearningBrief- MERL researcher, Oncel Tuzel, gave a keynote talk at 2016 International Symposium on Visual Computing in Las Vegas, Dec. 16, 2015. The talk was titled: "Machine vision for robotic bin-picking: Sensors and algorithms" and reviewed MERL's research in the application of 2D and 3D sensing and machine learning to the problem of general pose estimation.
The talk abstract was: For over four years, at MERL, we have worked on the robot "bin-picking" problem: using a 2D or 3D camera to look into a bin of parts and determine the pose, 3D rotation and translation, of a good candidate to pick up. We have solved the problem several different ways with several different sensors. I will briefly describe the sensors and the algorithms. In the first half of the talk, I will describe the Multi-Flash camera, a 2D camera with 8 flashes, and explain how this inexpensive camera design is used to extract robust geometric features, depth edges and specular edges, from the parts in a cluttered bin. I will present two pose estimation algorithms, (1) Fast directional chamfer matching--a sub-linear time line matching algorithm and (2) specular line reconstruction, for fast and robust pose estimation of parts with different surface characteristics. In the second half of the talk, I will present a voting-based pose estimation algorithm applicable to 3D sensors. We represent three-dimensional objects using a set of oriented point pair features: surface points with normals and boundary points with directions. I will describe a max-margin learning framework to identify discriminative features on the surface of the objects. The algorithm selects and ranks features according to their importance for the specified task which leads to improved accuracy and reduced computational cost.
- MERL researcher, Oncel Tuzel, gave a keynote talk at 2016 International Symposium on Visual Computing in Las Vegas, Dec. 16, 2015. The talk was titled: "Machine vision for robotic bin-picking: Sensors and algorithms" and reviewed MERL's research in the application of 2D and 3D sensing and machine learning to the problem of general pose estimation.
-
NEWS ICRA 2011: 2 publications by Yuichi Taguchi, Srikumar Ramalingam and C. Oncel Tuzel Date: May 9, 2011
Where: IEEE International Conference on Robotics and Automation (ICRA)
Research Area: Computer VisionBrief- The papers "Pose Estimation using Both Points and Lines for Geo-Localization" by Ramalingam, S., Bouaziz, S. and Sturm, P. and "Finding a Needle in a Specular Haystack" by Shroff, N., Taguchi, Y., Tuzel, O., Veeraraghavan, A., Ramalingam, S. and Okuda, H. were presented at the IEEE International Conference on Robotics and Automation (ICRA).